(253) 922-3090 | FAQ
Our products are built in the United States and, as our customers can attest to, have a lifetime value.
Our mission is simple: We never waver around our commitment to providing the highest level of quality, timely delivery of products, and superior customer service. We hold true to this in every decision we make.
Take your machining to a whole new level.
Increase your productivity output with these advantages.
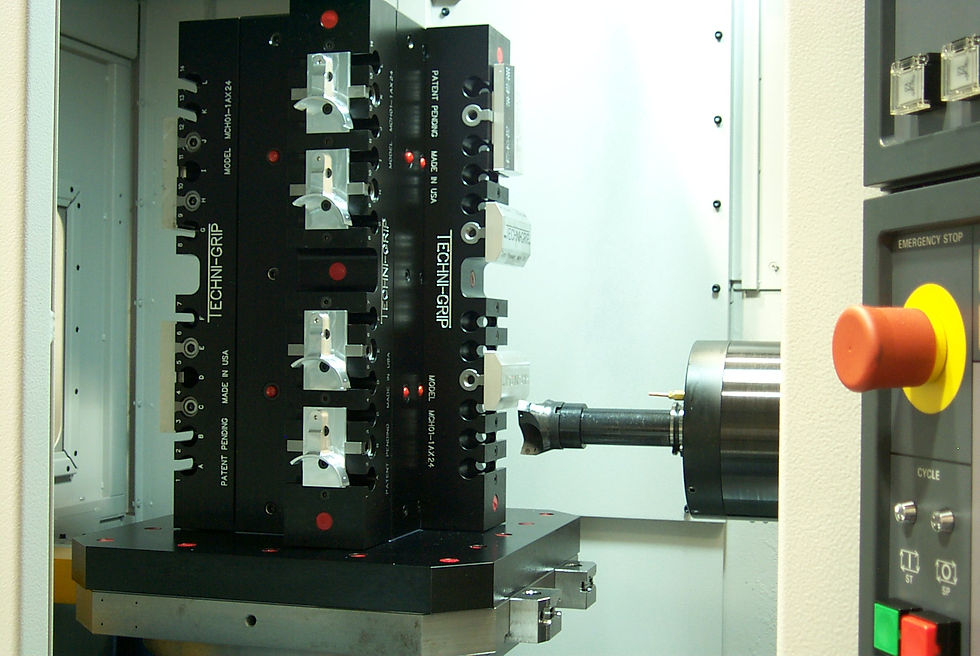
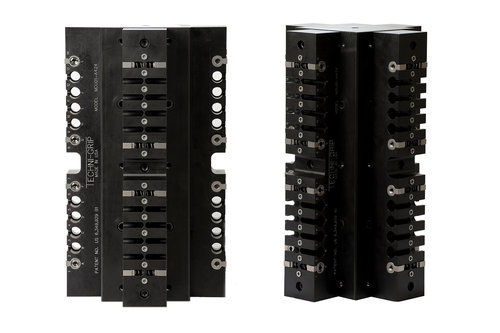

Techni-Grip is a leading workholding product manufacturer located in the Pacific Northwest. Our company was born in a machine shop. You probably can relate to how our story begins; we faced several complex workholding challenges that most CNC millwork creates. A team of engineers and designers set out to solve it. Many renditions later and after multiple testing scenarios, we had the final product. We used it in our business with much success when we realized our fellow estimators, programmers, machine operators and inspectors could benefit from it as well. Our Techni-Grip Systems meet you where you are at with any of your workholding and project requirements with results that promote your profitability and streamline your machining applications.

“I had a very large part out of aluminum (stock size (14 Feetx 12” x 3”). Because of the large amount of material being removed and the geometric shape not being square, we made this in 10 setups where it was flipped around in vises for a final cycle time of 40 hours per part.
The scrap rate due to setup error was over 50%. I had to create a business analysis and ROI to warrant the expense of the Techni-Grip vises and bases along with the 100 hours of programming to start from scratch. The results were 5 setups and a 12-hour run time with no scrap.”
Jeremie G.
Techni-Grip Advantages
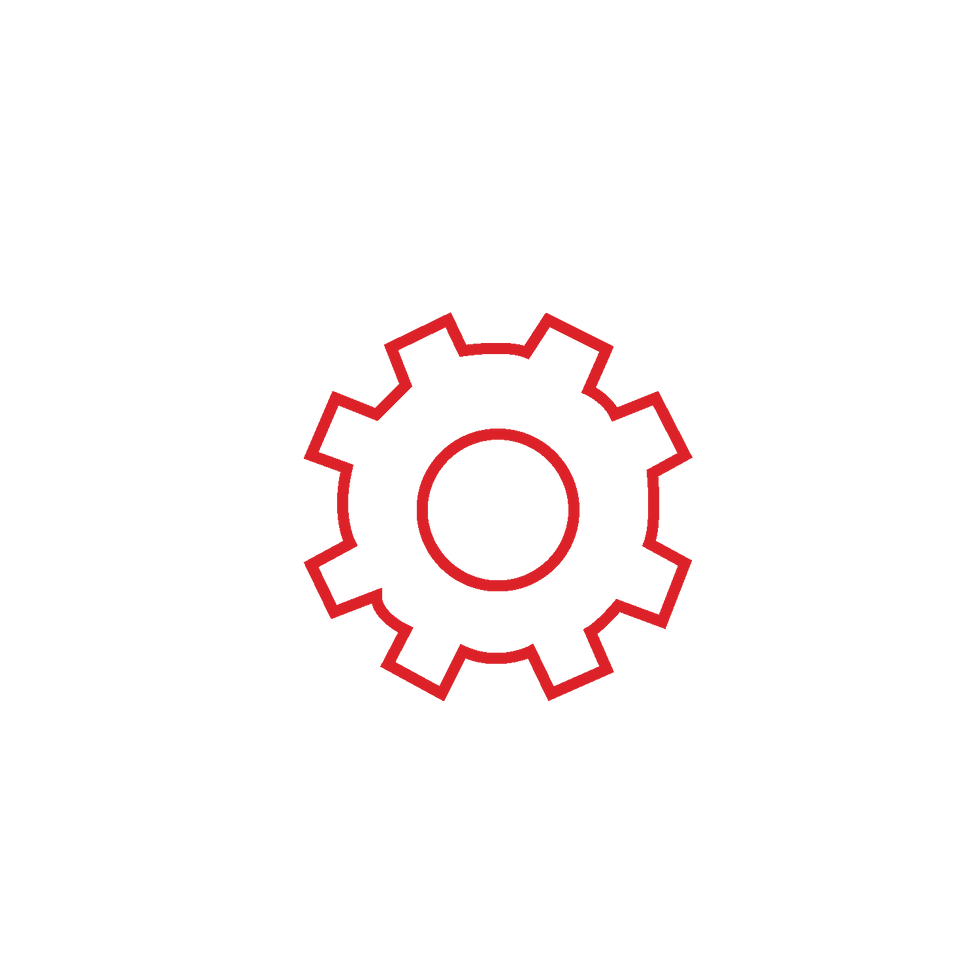
Standardization
-
All stock is prepped using the same method
-
All jobs are set up the same
-
All parts are held the same

Simplification
-
Work shifts and ‘Z’ shifts never change
-
Extensive documentation is eliminated
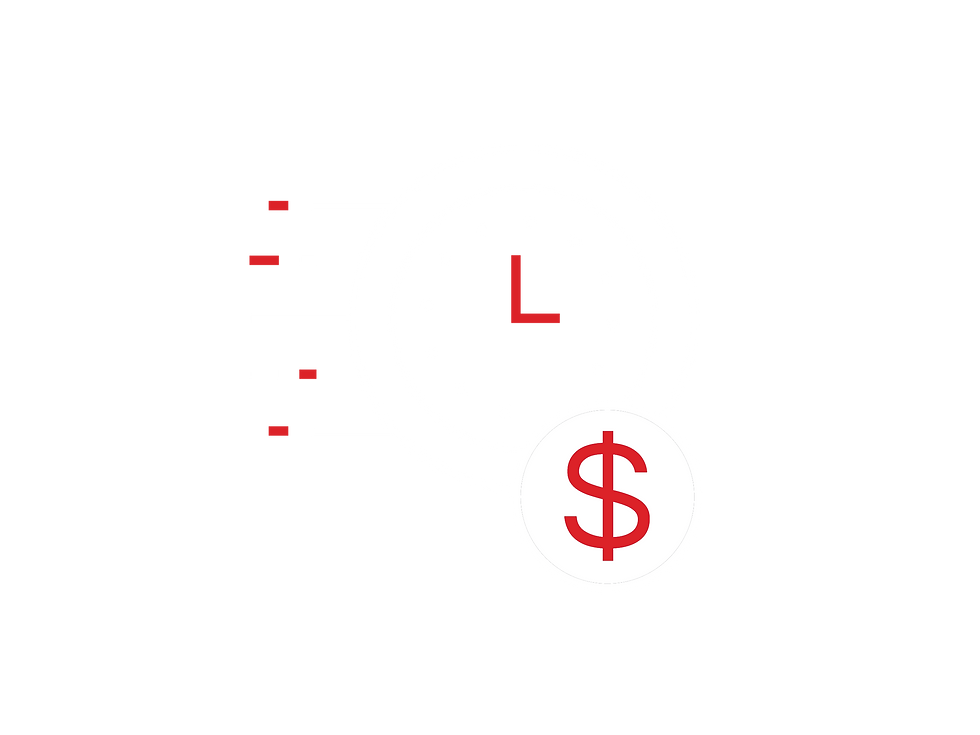
Time Reduction
-
Eliminates the following:
-
changing jaws
-
parallels and spreaders
-
milling step jaws and dovetail jaws
-
constructing work stops or programmable stops
-
maintenance, cleaning and organizing of shop aids
-
-
Increases stock removal capabilities
-
Multiple parts can be set up on a single unit
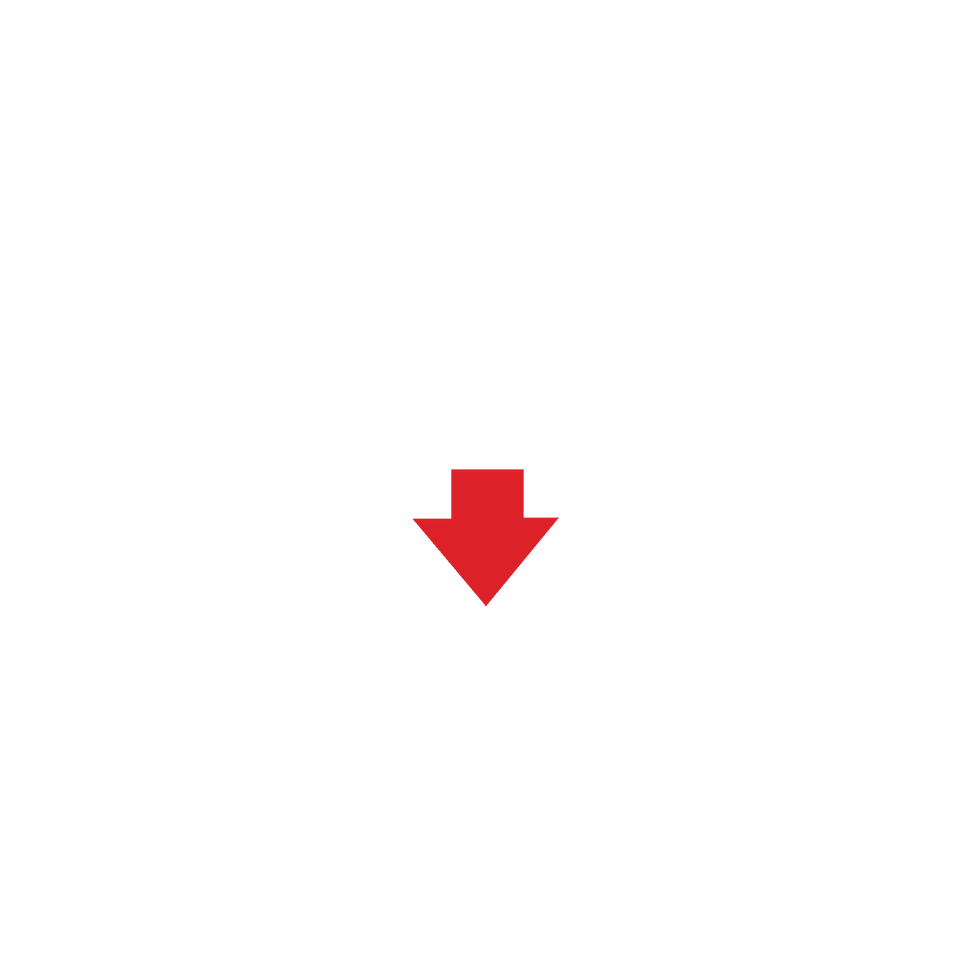
Scrap Reduction
-
Eliminates dimensional distortion in parts caused by vise pressure while running
-
No air under parts
-
Eliminates scrap generated by parts coming loose while running.
-
Allows precise relocation of parts should rework be required or if removed prematurely

Cost Reduction
-
Eliminates tool and machine damage from parts coming loose in a cut
-
Eliminates the need to buy and repair expensive vises
-
Only 0.125" excess (max) stock is required to hold parts
-
Stock can be prepped off-line through unskilled labor
-
Minimal training is required to load and unload parts